Previous lessons: Center of gravity
This section is divided into two sections. One for parents and one for the kids.
Parents:
Drag is the friction caused by the air the Pinewood Derby cars travel through. It is the following calculation:

rho (that little p) is the density of air (1.1644 kg/cubic meter, give or take depending on temperature and humidity)
v is the relative velocity of the object (the cars on our track travelled at about 4.0 meters/second)
C(d) is the drag coefficient of your car (how aerodynamic it is). A typical pinewood derby car should be around = 0.4, but you can do better. Here is a sample of real car's C(d):
http://en.wikipedia.org/wiki/Automobile_drag_coefficient
You can see the drag coefficients on real cars. Notice that F1 cars and other high performance cars have high drag coefficients. All those spoilers and airdams are mean to cause friction to cause imbalance of air flows to keep the car on the ground, not flying off of it, because the added power via traction far offsets any advantage of aerodynamics. So, 0.4 is a nice average car. You can probably get much lower than that having a flat car, closer to 0.2.
There are two things you can control when designing you car: the C(d) and the A. A is easier.
Adjusting "A"
Think of your car in cross sections, slicing it into slices like a sausage. Think of the thickest slice of your car. That is your A. Thus, it is best to have your back end be the thicker part because it will hold your weights. But make it as small as possible.Here is a big design difference. If you are like 95% of the Dads out there, you will take a 3/8" drillbit and drill holes in the back to slide in the weights. This is not going to win the race.
Your zinc weights are surrounded by high volume/low-density pinewood. If you can afford it, you want to carve out a pocket to fit your weights into it. Pine is very brittle, so you will need a way to carve out a pocket. I recommend a Dremel. You can get one for about $80. Get a grinding bit. They come standard in most Dremel kits and are usually pink or white. Then carve away to make a pocket. Sand your back and side walls very thin, but make an area for your axles to go through in the bottom. So there will literally be a flat step to hammer in your axles, but the step is flat so you can stack your weights on. Don't drill out the pocket too big. Make it big enough to fit two rows of weights. You will need to adjust the size later. You will need to rough cut your car and do the finer cuts to see how much weight you will need in the back. A key is to not leave the air pockets empty. Fill them with tungsten sand. If you don't have that, do it with iron filings. Don't have that? Fill it will beach sand, which isn't very dense, but it is better than air. So now you have a flat "pickup truck" in the back, where you will put a balsa top on it. You then carve the front end to be lighter, but with an eye to have a low C(d).
I have done the math and stacking all your weights in the back so that it is superback-end loaded is more than offset by the drag. Do yourself a favor and stack the weights lower. For tungsten weights, that is just a matter of putting them into 2 rows.
Adjusting C(d)
Think of all the wind tunnel tests that you have seen. A baseball has bad aerodynamics because it is round. Sure, it's better than throwing a tree branch, but it has all sorts of air distrbances coming off the back. This is what causes the baseballs to move and why there are so many different types of pitches in baseball.
Now think of a picture of car with smoke tracers. One smoke trail smashes into the front of the car and has to go around the car. The front has to be that shape because it is impractical to put a bullet cone on the front of the car. The rest of the smoke trails slip over the sleek top, but cause distrbance behind the car, which causes friction. That shape has to be there because it is impractical to have a tail cone to gently let the air slide back into place rather than just slam into the vaccuum caused by the car trunk leaving. That's why a submarine is shaped like it is.

And forget all the cool but bumpy details like spoilers, fenders, cockpits, and flared pilons.
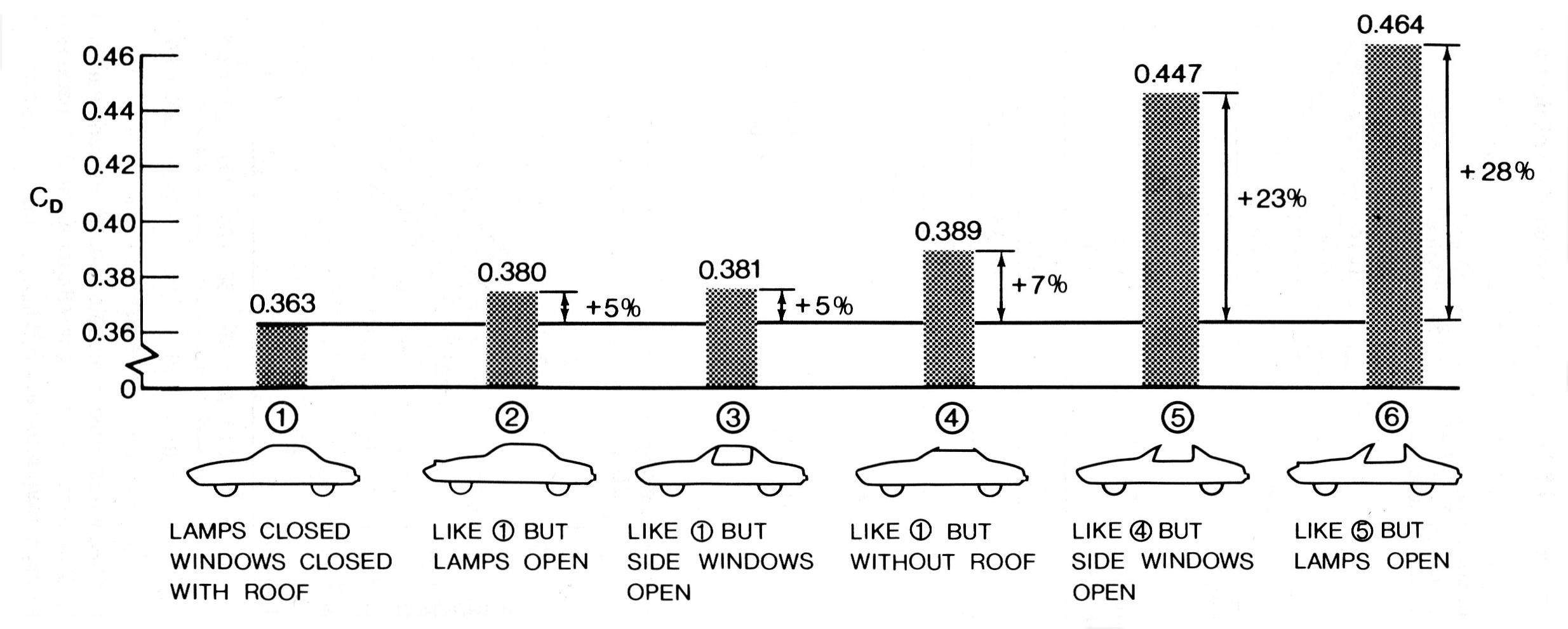
My son is going with a successful design that carved out a bunch of the weight in the front, leaving a giant hole in between where front axle and the back weight pocket went. It looks cool and it is easy to execute. However, I imagine that air rides over the front, slams together in the hole again, and then has to ride over the weight pocket again. He's going with the same design, simply because he can. I think that is exactly what he should do because ultimately, he has to be able to build the car - not me. I only counsel him on physics and design.
I am competing in the open class for Dads. I am building a car that reaches a sharp point in the front and then gently slopes to the back weight pocket. No steep rises or bumps to make C(d) high. And generally wedge shaped to minimize A. I am letting the air slam behind it with a flat tail-end because I have calculated that the superior center of gravity is worth it. I am removing almost all of the weight up front by carving out the middle, leaving a lattice of cross bars for support, but otherwise hollow. I am then adding a balsa nose cone and a thin balsa top. I will have a mimimum C(d) and minimum A that still allows me to have my center of gravity slightly in front of my rear axle.
No comments:
Post a Comment